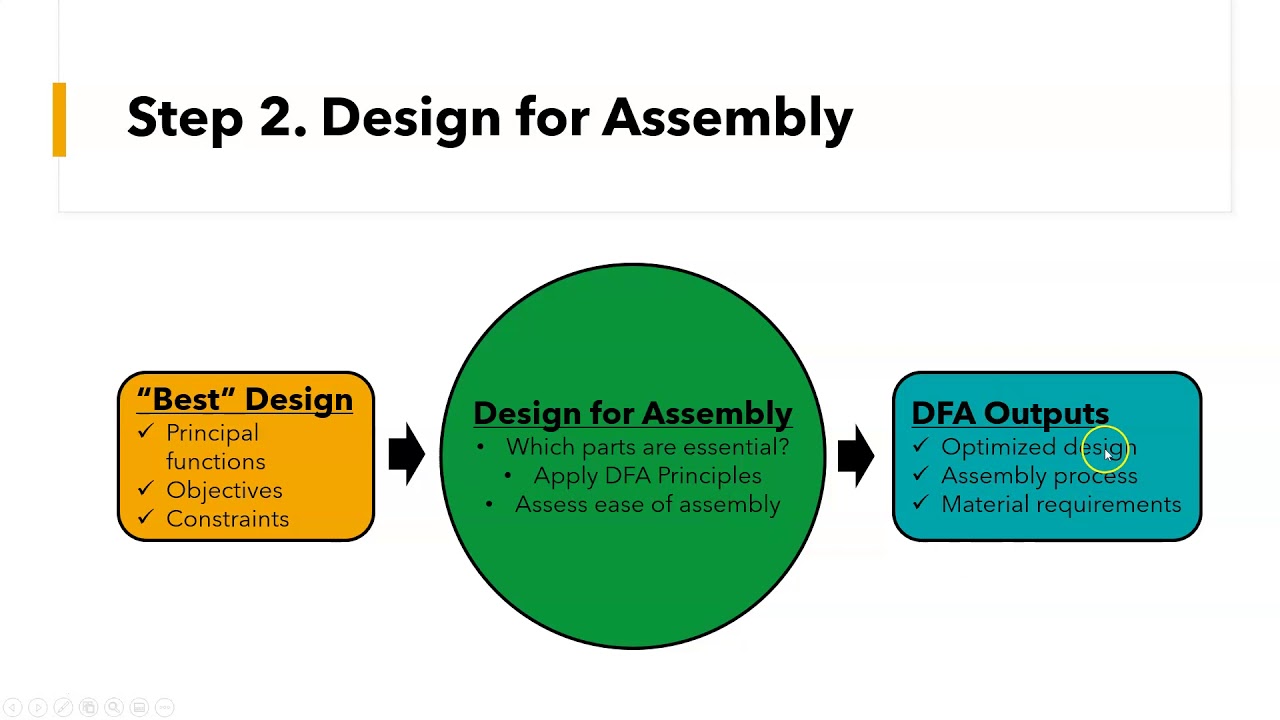
Create articles from any YouTube video or use our API to get YouTube transcriptions
Start for freeIntroduction to Design for Manufacturing and Assembly
Design for Manufacturing and Assembly (DFMA) is a crucial engineering methodology that aims to optimize product design for efficient manufacturing and assembly processes. By implementing DFMA principles early in the design stage, companies can significantly reduce costs, simplify production, and improve overall product quality.
In this comprehensive guide, we'll explore the key concepts of DFMA, its benefits, and how to apply these principles effectively in your product development process.
Understanding DFMA
DFMA is composed of two main components:
-
Design for Manufacturing (DFM): This methodology focuses on designing parts so that they can be manufactured as easily and inexpensively as possible while meeting functional requirements.
-
Design for Assembly (DFA): This approach aims to design parts in a way that simplifies their assembly into the final product, reducing time and costs associated with the assembly process.
By combining these two methodologies, DFMA provides a holistic approach to product design that considers both manufacturing and assembly aspects from the earliest stages of development.
The Importance of DFMA in Product Development
Implementing DFMA principles offers numerous benefits for companies:
-
Cost reduction: By simplifying product structure and optimizing manufacturing processes, DFMA can significantly lower production costs.
-
Improved quality: Streamlined designs with fewer parts are generally more reliable and easier to maintain.
-
Faster time-to-market: By addressing potential manufacturing and assembly issues early in the design process, companies can avoid costly redesigns and delays later on.
-
Enhanced competitiveness: DFMA provides tools for benchmarking against competitors and negotiating supplier contracts more effectively.
-
Better resource utilization: Simplified designs often require fewer materials and less energy to produce, contributing to sustainability goals.
Key Principles of Design for Assembly (DFA)
Design for Assembly focuses on creating products that are easy to assemble, whether manually or through automated processes. Here are some essential DFA principles:
1. Reduce Part Count
One of the most fundamental principles of DFA is to minimize the number of parts in a product. Fewer parts generally lead to:
- Shorter assembly times
- Lower costs
- Improved reliability
- Simplified inventory management
Designers should critically evaluate each part and ask if it's truly necessary or if its function can be integrated into another component.
2. Standardize and Use Common Parts
Using standard, off-the-shelf components wherever possible offers several advantages:
- Reduced inventory complexity
- Lower procurement costs
- Improved availability of parts
- Simplified maintenance and repair
3. Design for Top-Down Assembly
When designing the assembly process, aim for a top-down approach where parts are added from above. This method:
- Utilizes gravity to assist in the assembly process
- Reduces the need for reorientation during assembly
- Simplifies both manual and automated assembly processes
4. Incorporate Self-Locating Features
Design parts with features that help them align and position themselves correctly during assembly:
- Chamfers and tapers can guide parts into place
- Asymmetrical features can prevent incorrect orientation
- Self-aligning connectors reduce the need for precise manipulation
5. Minimize Reorientation
Each time a part or partially assembled product needs to be reoriented, it adds time and complexity to the assembly process. Design your product so that:
- Parts can be added from a single direction
- The need to flip or rotate the assembly is minimized
- Subassemblies can be completed separately and easily integrated
6. Ensure Accessibility
Make sure that all areas requiring assembly operations are easily accessible:
- Avoid designs where one part obstructs access to another
- Ensure sufficient space for tools or automated equipment
- Consider the ergonomics of manual assembly processes
7. Design for Ease of Handling
Parts should be designed to be easily grasped and manipulated:
- Avoid parts that are too small, slippery, or flexible
- Design parts with obvious grasping points
- Consider how parts will be presented to the assembly line (e.g., in bulk or oriented)
8. Prevent Assembly Errors
Incorporate features that make it difficult or impossible to assemble parts incorrectly:
- Use asymmetrical features for parts that must be oriented a specific way
- Implement error-proofing techniques (poka-yoke)
- Provide clear visual or tactile cues for correct assembly
Key Principles of Design for Manufacturing (DFM)
While DFA focuses on the assembly process, DFM principles aim to optimize the manufacturing of individual parts. Here are some key DFM guidelines:
1. Simplify Part Geometry
Complex part geometries often require more sophisticated and expensive manufacturing processes. Simplifying part geometry can:
- Reduce manufacturing time and cost
- Improve part quality and consistency
- Allow for the use of simpler, more widely available manufacturing processes
2. Design for Ease of Fabrication
Consider the manufacturing process when designing parts:
- Avoid features that require expensive or time-consuming operations
- Design parts that can be produced using standard tooling
- Minimize the need for secondary operations (e.g., finishing, deburring)
3. Specify Appropriate Tolerances
Overly tight tolerances can significantly increase manufacturing costs without necessarily improving product performance:
- Specify the loosest possible tolerances that still meet functional requirements
- Consider the capabilities of the intended manufacturing process when specifying tolerances
- Use standard tolerances where possible to avoid custom tooling or processes
4. Design for Minimal Material Usage
Optimizing material usage can reduce costs and improve sustainability:
- Use lightweight materials where appropriate
- Design parts to minimize waste during manufacturing
- Consider using near-net-shape manufacturing processes
5. Consider Manufacturing Process Capabilities
Each manufacturing process has its own set of capabilities and limitations:
- Choose materials that are compatible with the intended manufacturing process
- Design parts to take advantage of process-specific capabilities (e.g., draft angles for casting)
- Avoid features that are difficult or impossible to produce with the chosen process
6. Design for Automated Manufacturing
If high-volume production is anticipated, design parts with automation in mind:
- Ensure parts can be easily handled by robots or automated equipment
- Design features that facilitate automated inspection
- Consider how parts will be oriented and fed into automated machinery
7. Minimize Secondary Operations
Secondary operations add time and cost to the manufacturing process:
- Design parts to achieve the required surface finish directly from the primary manufacturing process
- Integrate features to eliminate the need for additional machining or finishing steps
- Consider alternative manufacturing processes that can produce the desired features in a single operation
8. Design for Scalability
Consider how the manufacturing process might need to scale as production volumes increase:
- Design parts that can be produced using both low and high-volume manufacturing methods
- Consider modular designs that allow for easy scaling of production
- Plan for potential automation of manual processes as volumes increase
Implementing DFMA in the Design Process
To effectively implement DFMA principles, they should be integrated throughout the product development process:
1. Concept Design Stage
During the initial concept design:
- Consider manufacturing and assembly constraints when generating ideas
- Evaluate concepts based on their potential for efficient manufacturing and assembly
- Involve manufacturing engineers and production staff in concept reviews
2. Detailed Design Stage
As the design is refined:
- Apply DFA principles to optimize the overall product structure
- Use DFM guidelines to detail individual part designs
- Conduct DFMA analyses to quantify potential improvements
3. Prototyping and Testing
During prototyping:
- Use prototypes to validate both function and manufacturability
- Identify and address any assembly or manufacturing issues
- Refine the design based on prototype feedback
4. Production Planning
As production is planned:
- Collaborate with manufacturing teams to optimize production processes
- Develop assembly instructions and training materials
- Plan for continuous improvement based on production feedback
Tools and Techniques for DFMA
Several tools and techniques can assist in applying DFMA principles:
1. DFMA Software
Specialized software tools can help analyze designs for manufacturability and assembly efficiency:
- Provide cost estimates based on part features and manufacturing processes
- Suggest design improvements to reduce costs or simplify assembly
- Allow for comparison of different design alternatives
2. Design Reviews
Regular design reviews with cross-functional teams can help identify opportunities for improvement:
- Include representatives from design, manufacturing, and quality assurance
- Use structured checklists to ensure all DFMA principles are considered
- Document and track action items for design improvements
3. Failure Mode and Effects Analysis (FMEA)
FMEA can help identify potential issues in both the product design and manufacturing process:
- Systematically analyze potential failure modes
- Prioritize risks based on severity, occurrence, and detectability
- Develop preventive measures to address high-priority risks
4. Value Engineering
Value engineering techniques can help optimize the balance between function and cost:
- Analyze the functions of each component or feature
- Identify opportunities to eliminate unnecessary functions or combine features
- Explore alternative materials or manufacturing processes to reduce costs
5. Rapid Prototyping
Modern rapid prototyping technologies allow for quick iteration and validation of designs:
- Use 3D printing to create physical prototypes for assembly testing
- Validate manufacturing processes with small-batch production runs
- Iterate quickly based on prototype feedback
Challenges in Implementing DFMA
While the benefits of DFMA are clear, there can be challenges in its implementation:
1. Resistance to Change
Designers and engineers may be resistant to changing established design practices:
- Provide training and education on DFMA principles and benefits
- Demonstrate success stories and quantify improvements
- Encourage a culture of continuous improvement
2. Time Constraints
The pressure to bring products to market quickly can make it tempting to skip DFMA analyses:
- Integrate DFMA tools and processes into the standard design workflow
- Demonstrate how DFMA can actually reduce overall development time by preventing late-stage issues
- Allocate sufficient time for DFMA activities in project schedules
3. Balancing DFMA with Other Design Requirements
Sometimes, DFMA principles may conflict with other design goals:
- Develop clear prioritization guidelines for different design requirements
- Use trade-off analyses to find optimal solutions
- Involve stakeholders from different departments in decision-making
4. Limited Manufacturing Knowledge
Designers may not have in-depth knowledge of manufacturing processes:
- Provide ongoing training on manufacturing technologies and capabilities
- Foster collaboration between design and manufacturing teams
- Consider embedding manufacturing engineers within design teams
Case Studies: DFMA Success Stories
Numerous companies have successfully implemented DFMA principles to achieve significant improvements:
Case Study 1: Automotive Component Redesign
A major automotive supplier redesigned a complex assembly using DFMA principles:
- Reduced part count from 19 to 8
- Decreased assembly time from 227 seconds to 84 seconds
- Lowered assembly cost by 33%
This redesign not only reduced costs but also improved reliability and simplified inventory management.
Case Study 2: Consumer Electronics Optimization
A consumer electronics manufacturer applied DFMA to a new product line:
- Standardized fasteners across multiple products
- Redesigned plastic components to incorporate snap-fit assembly
- Optimized part geometry for injection molding
These changes resulted in a 25% reduction in assembly time and a 15% decrease in overall product cost.
Case Study 3: Medical Device Improvement
A medical device company used DFMA to redesign a complex surgical instrument:
- Reduced the number of unique parts by 40%
- Simplified the assembly process, reducing assembly time by 50%
- Improved product reliability by eliminating potential failure points
The redesign not only reduced manufacturing costs but also improved the product's performance and ease of use for medical professionals.
Future Trends in DFMA
As manufacturing technologies and design tools continue to evolve, several trends are shaping the future of DFMA:
1. Integration with Digital Twin Technology
Digital twins - virtual representations of physical products - are becoming increasingly sophisticated:
- Allow for real-time simulation of manufacturing and assembly processes
- Enable optimization of designs based on actual production data
- Facilitate predictive maintenance and continuous improvement
2. Artificial Intelligence and Machine Learning
AI and ML technologies are being applied to DFMA:
- Automated design optimization based on manufacturability criteria
- Predictive analytics for identifying potential manufacturing issues
- Generative design tools that incorporate DFMA principles
3. Advanced Materials and Manufacturing Processes
New materials and manufacturing technologies are expanding design possibilities:
- Additive manufacturing (3D printing) enabling complex geometries
- Composite materials offering new strength-to-weight ratios
- Smart materials with embedded sensors and actuators
4. Sustainability and Circular Economy
DFMA principles are being extended to consider the entire product lifecycle:
- Design for disassembly and recycling
- Consideration of environmental impact in material and process selection
- Integration of remanufacturing and refurbishment into product design
5. Increased Automation and Robotics
As manufacturing becomes increasingly automated, DFMA must adapt:
- Designing for robotic assembly and handling
- Incorporating sensors and feedback systems into products
- Optimizing designs for lights-out manufacturing
Conclusion
Design for Manufacturing and Assembly (DFMA) is a powerful methodology that can significantly improve product design, reduce costs, and enhance manufacturing efficiency. By applying DFMA principles early in the design process, companies can create products that are not only functional and appealing to customers but also optimized for efficient production.
Key takeaways from this guide include:
-
DFMA combines Design for Manufacturing (DFM) and Design for Assembly (DFA) principles to create a comprehensive approach to product design.
-
Implementing DFMA can lead to reduced costs, improved quality, faster time-to-market, and enhanced competitiveness.
-
Core DFA principles include reducing part count, standardizing components, and designing for easy handling and assembly.
-
DFM focuses on optimizing individual part designs for specific manufacturing processes, considering factors like material selection, tolerances, and process capabilities.
-
Successful implementation of DFMA requires integration throughout the design process, from concept development to production planning.
-
Various tools and techniques, including specialized software, design reviews, and rapid prototyping, can support DFMA implementation.
-
While challenges exist in adopting DFMA, many companies have achieved significant improvements through its application.
-
Future trends in DFMA include integration with digital twin technology, AI-driven optimization, and increased focus on sustainability.
By embracing DFMA principles and staying abreast of emerging trends, companies can position themselves for success in an increasingly competitive global manufacturing landscape. The key is to view DFMA not as a one-time effort, but as an ongoing process of continuous improvement that evolves with new technologies and market demands.
Article created from: https://www.youtube.com/watch?v=UAZPugxUpQE