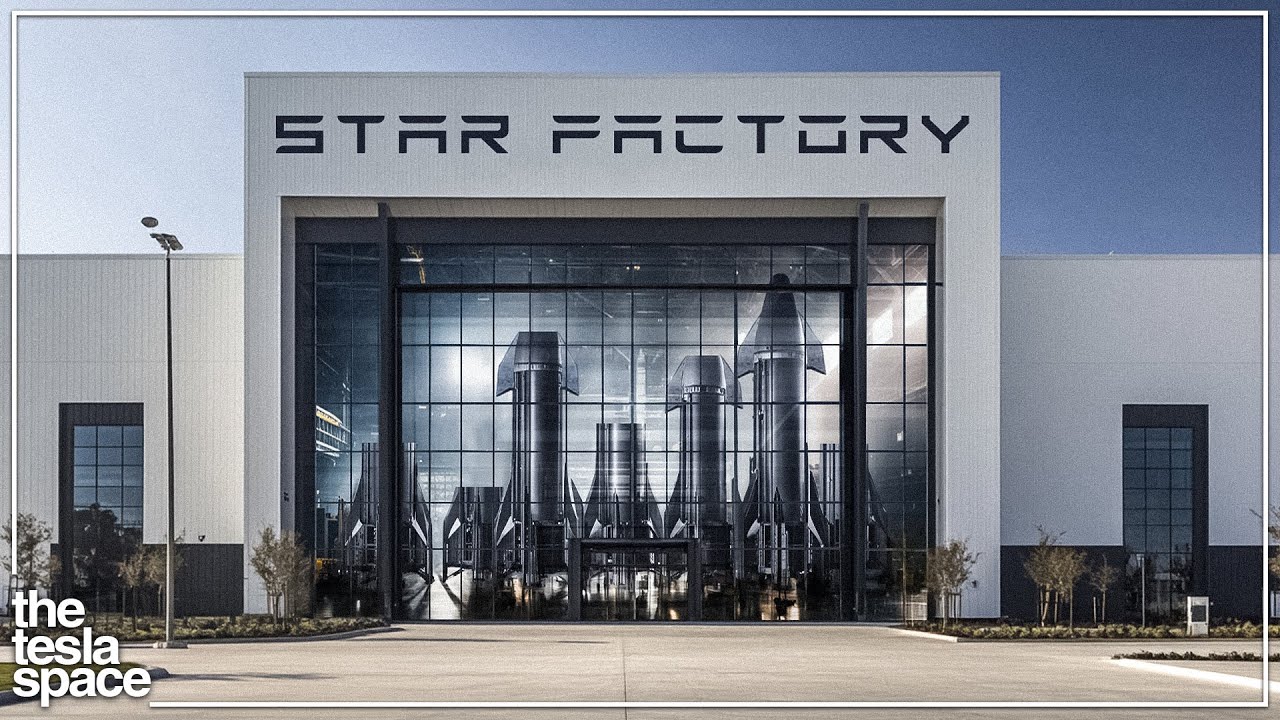
Create articles from any YouTube video or use our API to get YouTube transcriptions
Start for freeThe Birth of the Star Factory
In a groundbreaking move, SpaceX has constructed a massive Starship rocket factory at their Starbase Texas testing facility. This new production center, dubbed the Star Factory, represents a quantum leap in aerospace manufacturing capabilities. It's designed to mass-produce rockets with a level of speed and efficiency that far surpasses anything the industry has seen before.
Location and Evolution
The Star Factory is strategically positioned near the Starbase launch pad, which has been the site of the past four orbital flight tests. This location was previously home to three large tents where the team manufactured Starship B1, the rocket we've come to know through various tests and launches.
While the tent system allowed SpaceX to rapidly initiate Starship operations, it was far from ideal. Elon Musk described the early phase of Starship manufacturing as constantly battling mud, dust, and birds. However, the flexibility offered by the tents was crucial during the initial stages of development.
From Tents to Permanent Structure
The transition from tents to a permanent structure marks a significant milestone in Starship's development. The non-permanent nature of the tents allowed for rapid design changes and manufacturing process adjustments. This flexibility was essential, as Starship was an unprecedented project with no existing blueprint to follow.
The result of this trial-and-error approach was a series of Starship rockets that often differed significantly from one build to the next. These variations were reflected in the varying degrees of success (or failure) observed during test flights and launches.
Starship V2: The Next Generation
After years of experimentation, explosions, and incremental improvements, SpaceX has finally arrived at a Starship design they believe can achieve their ambitious goals. Enter Starship V2, also known as Block 2.
Key Features of Starship V2
-
Height: The new version will be approximately 2 meters (6 feet) taller than its predecessor.
-
Nose Cone and Aero Flaps: The most significant changes are in the nose cone design and the configuration of the aero flaps.
-
Flap Design: The V2 nose flaps are more diamond-shaped with a distinct point at the trailing edge. This design helps push shock waves from the atmosphere away from the ship's body, preventing excessive pressure buildup under the wing.
-
Flap Positioning: The flaps are mounted higher on the nose, increasing their leverage on the ship. They're also positioned further back on the leeward side of the hull, reducing hot plasma buildup during re-entry.
-
Flap Profile: The new flaps are about half as thick as the originals, with a much lower-profile hinge mechanism.
-
Heat Shield: The V2 nose cone features more extensive heat shielding, with tiles wrapping around to cover more of the leeward side of the vehicle.
-
Insulation: Improved insulation is crucial, especially around the nose cone, which houses a header tank storing propellant for the landing burn.
The Star Factory Manufacturing Process
The manufacturing process employed in the Star Factory is a departure from traditional assembly line methods. Elon Musk describes it as a "linear adjacent flow," a term he seems to have coined himself.
Understanding Linear Adjacent Flow
This approach appears to be the opposite of the standard moving assembly line pioneered by Henry Ford a century ago. Instead of a product moving down a conveyor belt and gradually having components added, the Star Factory uses a system similar to Tesla's "unboxed manufacturing" process.
In this method, separate segments of the rocket are built in parallel before being brought together for final assembly. This approach allows for greater efficiency and flexibility in the manufacturing process.
Key Principles of Star Factory Production
-
Parallel Manufacturing: Different sections of the rocket are built simultaneously on adjacent production lines.
-
Specialized Stations: The production line consists of various stations, each dedicated to specific tasks.
-
Continuous Motion: The tempo at which products move from one station to the next is crucial, with an emphasis on minimizing downtime.
-
Stationary Line: Unlike traditional assembly lines, the production line itself doesn't move.
The Production Process in Detail
-
Steel Preparation: The process begins with giant rolls of stainless steel being cut and welded into rings for the body segments.
-
Nose Cone Formation: The pointy segment of the nose cone is created using a hydroforming machine to press stainless steel into the required shape.
-
Tank Dome Creation: Similar hydroforming techniques are used to create the round domes that form the tops and bottoms of the ship's fuel tanks.
-
Ring Assembly: Rings are stacked and welded together into segments, typically comprising 3 to 5 rings per section.
-
Progressive Assembly: As components move down the production line, they gradually take on more recognizable rocket shapes.
-
Specialized Stations: Different stations handle tasks such as mounting and checking heat shield tiles, fitting and plumbing fuel tanks, and building thruster assemblies.
-
Segmented Construction: Due to height limitations, the Star Factory builds the top, bottom, and middle sections of Starship separately.
-
Final Assembly: The completed segments are transported to the Mega Bay for final stacking, Raptor engine installation, and finishing touches.
Production Goals and Future Expansion
Elon Musk has set ambitious production targets for Starship:
-
Short-term Goal: The existing Star Factory aims to build around 100 rockets per year, or one every 3 days.
-
Long-term Vision: Musk envisions building 1,000 Starships per year in the future, which would support the Mars city-building phase of SpaceX's plans.
-
Expansion Plans: SpaceX is already laying the foundation for Star Factory 2 at their Cape Canaveral property.
-
Potential Output: With a second Star Factory, production could increase to one rocket every 1.5 days, potentially reaching one rocket per day with further efficiency improvements.
Comparison to Current Production
To put these goals in perspective, SpaceX is currently producing just under 200 Falcon 9 upper stage platforms per year, with plans to exceed 200 next year. While the Falcon upper stage is a simpler construction than Starship, this demonstrates SpaceX's ability to scale up production significantly.
The Impact of Mass Production
The ability to mass-produce Starships at this scale could have profound implications for space exploration and colonization efforts:
-
Reduced Costs: Economies of scale could dramatically lower the cost per launch, making space access more affordable.
-
Increased Launch Frequency: A larger fleet of available rockets could support more frequent launches and missions.
-
Rapid Iteration: The ability to quickly produce new rockets allows for faster implementation of design improvements and innovations.
-
Support for Mars Missions: A large fleet of Starships is crucial for Musk's vision of establishing a self-sustaining city on Mars.
-
Earth-to-Earth Transport: Mass production could support the development of point-to-point transportation on Earth using Starship.
Challenges and Considerations
While the Star Factory represents a significant advancement in rocket manufacturing, several challenges and considerations remain:
-
Quality Control: Maintaining consistent quality across high-volume production will be crucial.
-
Supply Chain Management: Ensuring a steady supply of materials and components for such high-volume production could be challenging.
-
Environmental Impact: The environmental implications of mass-producing and launching large numbers of rockets need to be carefully considered.
-
Regulatory Hurdles: Increased production and launch frequencies may face regulatory challenges and require new frameworks.
-
Market Demand: The success of this endeavor depends on whether there's sufficient demand for such a high number of launches.
The Future of Rocket Manufacturing
The Star Factory represents a paradigm shift in how we approach rocket manufacturing. By applying principles from automotive mass production to the aerospace industry, SpaceX is paving the way for a future where space vehicles can be produced with the same efficiency as cars.
This approach could democratize access to space, making it more accessible and affordable for a wide range of applications, from scientific research to space tourism. As production scales up and costs come down, we may see a proliferation of space-based services and technologies that were previously economically unfeasible.
Moreover, the ability to rapidly produce and iterate on rocket designs could accelerate the pace of innovation in space technology. This could lead to faster development of more advanced propulsion systems, life support technologies, and other crucial components for deep space exploration.
Conclusion
SpaceX's Star Factory marks a new era in rocket manufacturing. By combining innovative design with efficient production methods, SpaceX is positioning itself to lead the charge in making space more accessible than ever before. As production ramps up and new factories come online, we may be witnessing the early stages of a revolution in space exploration and utilization.
The implications of this development extend far beyond just SpaceX or even the aerospace industry. Mass production of rockets could reshape our relationship with space, opening up new possibilities for scientific discovery, resource utilization, and even human habitation beyond Earth. As we watch the Star Factory take shape and begin operations, we're not just observing the birth of a new manufacturing facility – we're witnessing the dawn of a new space age.
Article created from: https://youtu.be/27PHT9K8izo?feature=shared