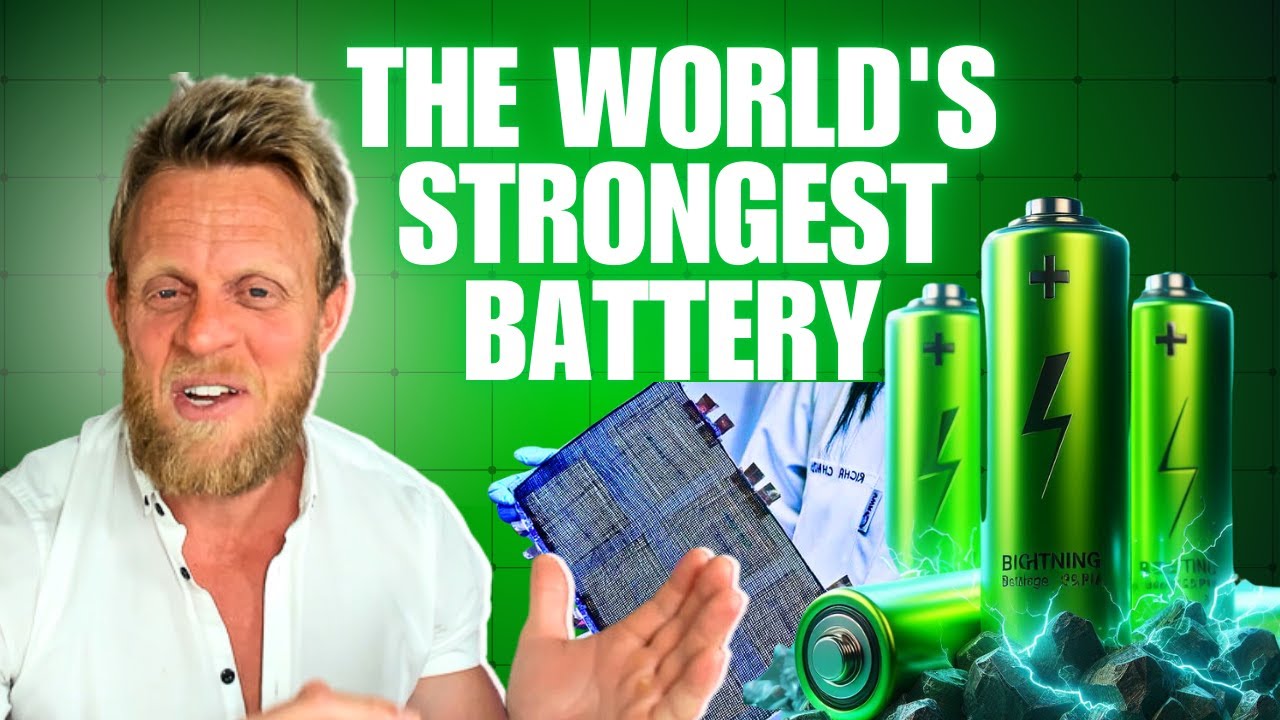
Create articles from any YouTube video or use our API to get YouTube transcriptions
Start for freeThe World's Strongest Structural Battery
In a groundbreaking development, researchers in Sweden have unveiled what is being hailed as the strongest functional structural battery in the world. This innovative device, characterized by an elastic modulus surpassing any previous design, was developed by Leif Asp and his team at Chalmers University of Technology. The implications of this breakthrough could be far-reaching, potentially revolutionizing the automotive industry and paving the way for lighter, more efficient electric vehicles (EVs).
Understanding Structural Batteries
Structural batteries represent an emerging technology that serves a dual purpose: storing electrical energy while simultaneously bearing mechanical loads. This unique characteristic makes them particularly valuable in applications where minimizing extra weight and volume associated with traditional batteries is crucial. By incorporating batteries into a vehicle's structural components, manufacturers can significantly enhance space efficiency and overall performance.
The Evolution of Structural Batteries
The journey towards creating the world's strongest structural battery has been marked by several key milestones:
-
2018 Breakthrough: Asp's team made significant progress in balancing the mechanical strength of highly ordered carbon fibers with the electrochemical properties of less ordered structures. This achievement earned them recognition in Physics World's top 10 breakthroughs of 2018.
-
First Generation (2021): The team unveiled their initial structural battery design, utilizing carbon fibers as the negative electrode and commercial lithium iron phosphate on aluminum foil as the positive electrode. This version offered a gravimetric energy density of 24 Wh/kg.
-
Second Generation (2023): Improvements in manufacturing techniques, particularly in resin distribution, led to enhanced mechanical strength and electrical conductivity.
-
Third Generation (Current): The latest iteration represents a significant leap forward, featuring an all-fiber structural battery with carbon fiber-based electrodes in both the positive and negative terminals.
Key Features of the World's Strongest Structural Battery
Carbon Fiber Technology
The use of carbon fiber technology is at the heart of this revolutionary battery design. By employing carbon fibers in both electrodes, the researchers have achieved a remarkable balance between mechanical strength and energy density. This approach addresses previous limitations associated with lithium iron phosphate positive electrodes.
Manufacturing Process
The manufacturing process involves several innovative techniques:
-
Electrooptic Deposition: The carbon fibers are coated with a layer of lithium iron phosphate using this advanced technique, which utilizes electric fields to deposit charged particles onto substrates.
-
Cellulose Separator: A thin cellulose separator is incorporated to further enhance the battery's energy density.
-
Infusion Technique: All components are embedded in the battery's structural electrolyte and cured in resin using an improved infusion technique developed for the second-generation battery.
Performance Metrics
The latest iteration of this structural battery boasts impressive performance metrics:
- Energy Density: 30 Wh/kg
- Elastic Modulus: Greater than 76 GPa (when tested parallel to carbon fibers)
- Efficiency: Nearly 100% efficiency in storing and releasing charge after 1,000 cycles
These figures represent a significant improvement over previous designs and set a new benchmark for structural battery technology.
Implications for the Automotive Industry
The development of this ultra-strong structural battery could have profound implications for the automotive industry, particularly in the realm of electric vehicles:
Enhanced Safety
Structural battery packs, like those pioneered by Tesla, have already demonstrated their value in improving crash safety ratings. The incorporation of even stronger carbon fiber-based structural batteries could further enhance vehicle safety, particularly in side-impact scenarios.
Improved Space Efficiency
As volumetric energy density in battery packs continues to improve (currently reaching 75-80% in modern EVs compared to about 50% a decade ago), stronger structural batteries could enable even greater space efficiency in vehicle design.
Weight Reduction
The use of carbon fiber in structural batteries could contribute to significant weight reductions in EVs, potentially improving range and overall performance.
Range Extension
The combination of improved space efficiency, weight reduction, and enhanced structural integrity could collectively contribute to extended range capabilities in electric vehicles.
Future Prospects and Ongoing Research
The research team behind this breakthrough is not resting on their laurels. They have ambitious goals for further improving their structural battery technology:
- Increased Strength: The team aims to develop structural battery cells with an elastic modulus exceeding 100 GPa.
- Higher Energy Density: Future iterations are expected to achieve energy densities surpassing 50 Wh/kg.
If these goals are realized, the potential applications extend beyond the automotive industry. We could see transformative impacts in various sectors:
- Consumer Electronics: Lighter, more durable laptops and portable devices.
- Aerospace: Improved efficiency in aircraft design and performance.
- Maritime: Enhanced capabilities for ships and marine vessels.
The Role of Carbon Fiber in Future Battery Technology
The heavy reliance on carbon fiber in this groundbreaking battery design raises interesting possibilities for the future of battery technology:
Cost-Effective Carbon Fiber Production
While carbon fiber has traditionally been associated with high costs, recent developments suggest that cost-effective production methods are emerging. Companies like Aptera are already incorporating carbon fiber extensively in their affordable electric vehicle designs.
Carbon Fiber Molding Techniques
Advanced carbon fiber molding techniques, similar to Tesla's Giga casting technology, could enable efficient and rapid manufacturing of large carbon fiber structural battery packs. This approach could combine the strength and lightweight properties of carbon fiber with the production efficiency of modern casting methods.
Integration with Existing Manufacturing Processes
The potential for integrating carbon fiber structural batteries into existing automotive manufacturing processes could accelerate adoption across the industry. As companies become more familiar with working with carbon fiber components, the transition to carbon fiber-based structural batteries could become more feasible.
Challenges and Considerations
Despite the promising advancements, there are several challenges and considerations to address:
Energy Density Limitations
While the strength-to-weight ratio of the new structural battery is impressive, its current energy density (30 Wh/kg) is significantly lower than conventional lithium-ion batteries used in EVs. Bridging this gap will be crucial for practical applications.
Scalability
Transitioning from laboratory prototypes to mass production presents numerous challenges. Researchers and manufacturers will need to develop scalable production methods that maintain the battery's exceptional properties.
Cost Considerations
The use of advanced materials like carbon fiber and specialized manufacturing processes could potentially increase production costs. Balancing performance improvements with economic viability will be essential for widespread adoption.
Regulatory Approval
As with any new automotive technology, extensive testing and regulatory approval processes will be necessary before these advanced structural batteries can be implemented in consumer vehicles.
Potential Impact on EV Design and Performance
The advent of ultra-strong structural batteries could lead to a paradigm shift in EV design and performance:
Innovative Vehicle Architectures
With batteries integrated into the vehicle's structure, designers could have more freedom to create innovative vehicle architectures that optimize space, aerodynamics, and functionality.
Improved Handling and Dynamics
The distribution of battery weight throughout the vehicle's structure could lead to improved weight distribution, potentially enhancing handling and overall driving dynamics.
Extended Range Capabilities
Lighter, more efficient vehicles with integrated structural batteries could achieve significantly extended range capabilities, addressing one of the primary concerns of potential EV adopters.
Enhanced Safety Features
The increased strength of carbon fiber structural batteries could allow for the incorporation of advanced safety features without compromising on weight or performance.
The Road Ahead: Integrating Research with Industry
For this breakthrough to transition from the laboratory to the automotive industry, several steps will be necessary:
Collaborative Research Initiatives
Partnerships between academic institutions, research laboratories, and automotive manufacturers will be crucial in adapting this technology for practical applications.
Prototype Development
Creating functional prototypes that demonstrate the real-world benefits of these advanced structural batteries will be a critical next step.
Manufacturing Process Optimization
Developing efficient, cost-effective manufacturing processes for carbon fiber structural batteries at scale will be essential for industry adoption.
Performance Testing and Validation
Extensive testing under various conditions will be necessary to validate the performance, safety, and longevity of these new battery systems in automotive applications.
Conclusion
The development of the world's strongest structural battery marks a significant milestone in the evolution of energy storage technology. By combining the mechanical strength of carbon fiber with advanced battery chemistry, researchers have opened up new possibilities for the future of electric vehicles and beyond.
While challenges remain in terms of energy density and scalability, the potential benefits of this technology are immense. From lighter, more efficient vehicles to improved safety and performance, the impact of these advanced structural batteries could be transformative.
As research continues and collaborations between academia and industry grow, we may be witnessing the early stages of a revolution in battery technology that could reshape the automotive landscape and accelerate the transition to sustainable transportation.
The journey from laboratory breakthrough to industry-wide implementation is often long and complex, but the potential rewards are substantial. As we look to the future, the integration of ultra-strong structural batteries into electric vehicles represents an exciting frontier in automotive innovation, promising a new era of safer, more efficient, and higher-performing electric vehicles.
Article created from: https://youtu.be/XRoJt57Oz_U?feature=shared