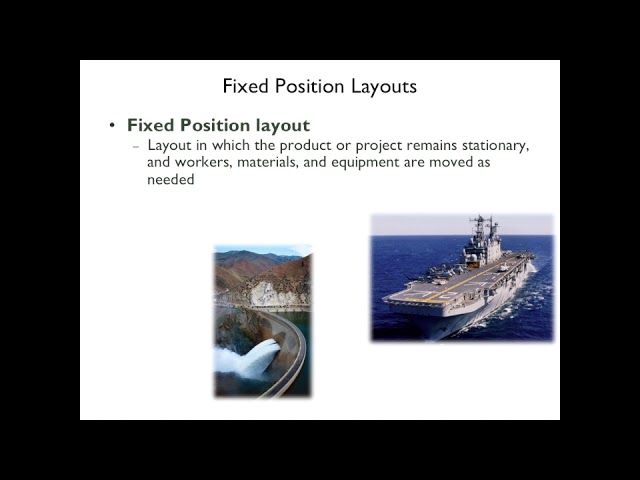
Create articles from any YouTube video or use our API to get YouTube transcriptions
Start for freeProcess Selection and Its Role in System Design
When it comes to system design, process selection is a crucial factor intertwined with capacity planning. It's essential to determine the required capacity and then design processes that align with that capacity. This includes considerations such as forecasting, product and service design, and the impact of technological advancements. The outcomes of process selection include the determination of facilities and equipment needs, layout planning, and work design.
Types of Processing
- Job Shop: Customized tasks with high flexibility but slow and costly per unit. Complex planning and scheduling are needed.
- Batch Processing: Semi-standard goods or services with better cost per unit and moderate scheduling complexity.
- Repetitive/Assembly Line: Standardized goods or services with a focus on repetition, low flexibility, and significant downtime costs.
- Continuous Processing: Highly standardized and efficient with high volume but rigid and costly to change.
The Importance of Planning Layouts
A well-planned layout is imperative to avoid inefficiency, high costs, bottlenecks, accidents, and morale issues. Layout changes might be necessary due to new product introductions, output modifications, method changes, environmental regulations, or legal requirements. The primary design objective is to ensure a smooth flow of work, material, and information, which supports goals like better quality, efficient space utilization, bottleneck avoidance, and minimized material handling costs.
Repetitive Processing and Product Layouts
An example of this is a food assembly line in restaurants like Chipotle, where each station adds components to the product. This type of layout can be adapted to both repetitive and continuous processes.
Non-Repetitive Process Layouts
This layout allows for a variety of processes and orders, such as different paths taken when registering for a class, where the order of departmental visits can vary based on the student's needs.
Fixed Position Layouts
Used in scenarios where the product is stationary, and workers, materials, and equipment are moved around, such as in dam maintenance or ship repairs.
Combination Layouts
Hospitals and supermarkets are examples where combination layouts are employed, mixing elements of process, product, and fixed position layouts to cater to specific needs.
Service Layouts and Their Unique Requirements
Service layouts differ due to factors like customer contact and customization levels. They include warehouse storage, retail, and office layouts. Quick oil change services are an example, where the layout is designed for efficiency, allowing customers to remain in their vehicles during the service.
Line Balancing Essentials
Line balancing aims to assign tasks to workstations in a way that each workstation has approximately equal time requirements. This improves labor and equipment efficiency and addresses fairness issues.
The Line Balancing Process
- Determine cycle time: The maximum time each workstation has to complete its tasks.
- Calculate output: Operating time per day divided by the cycle time.
- Workstation requirements: Based on desired output, determine the theoretical minimum number of workstations.
Efficiency Calculation
Efficiency is calculated by subtracting idle time from 100%. The goal is to minimize idle time to ensure that workstations are as balanced as possible, preventing disputes over workstation assignments.
In conclusion, understanding process selection, facility layout, and line balancing is fundamental for any business to optimize its operations and create a smooth, cost-effective workflow. These elements work together to enhance productivity, quality, and worker satisfaction while reducing costs and downtime.
For a deeper dive into process selection and facility layout, watch the full video here.