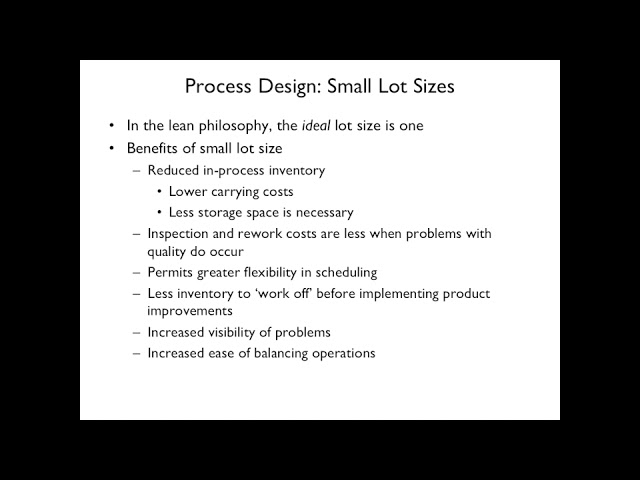
Create articles from any YouTube video or use our API to get YouTube transcriptions
Start for freeEmbracing Lean Operations: The Path to Enhanced Productivity and Quality
Lean operations signify a paradigm shift toward a more efficient and resource-conservative approach in business processes. This methodology focuses on flexibility and minimal resource usage, contrasting traditional systems. The key benefits of lean operations include:
- Increased productivity
- Lower costs
- Shorter cycle times
- Enhanced quality
Characteristics of Lean Systems
Lean systems are distinguished by their unique characteristics that pave the way for these benefits. These include:
- Waste Reduction: Eliminating non-value-adding activities.
- Continuous Improvement: Constantly refining processes.
- Team Utilization: Leveraging collaborative efforts for better results.
- Work Cells: Grouping related processes for efficiency.
- Visual Controls: Using visual signals to guide operations.
- High Quality: Emphasizing defect-free outcomes.
- Minimal Inventory: Keeping stock levels low to reduce costs.
- Demand-driven Output: Producing only what is needed.
- Quick Changeovers: Reducing downtime between production changes.
- Small Lot Sizes: Minimizing work-in-process and associated costs.
- Cultivating a Lean Culture: Ensuring everyone in the organization is aligned with lean principles.
The Five Core Principles of Lean
- Identify Customer Values: Understanding what the customer truly values.
- Value-Creating Processes: Focusing on processes that enhance value.
- Eliminate Waste: Removing unnecessary steps to create flow.
- Customer Demand Production: Only producing what customers need.
- Perfection Striving: Always aiming for continuous improvement.
Benefits and Risks of Lean Systems
While lean systems offer significant advantages, such as reduced waste, lower costs, and increased flexibility, they also come with risks:
- Increased Stress on Workers: Lean operations can put additional pressure on employees to maintain the flow.
- Fewer Resources in Case of Problems: Lean systems have less buffer to absorb disruptions.
- Supply Chain Vulnerabilities: Dependence on timely deliveries can lead to shutdowns if supply chains are disrupted.
Just-In-Time (JIT): The Synchronization of Supply and Demand
Just-In-Time, or JIT, is a system that coordinates the movement of goods and services precisely when they are needed, minimizing inventory levels and reducing waste. The JIT philosophy was developed by Toyota in the mid-1900s, aiming to eliminate waste from every aspect of the production process.
Supporting Goals for Lean
Three additional goals support the lean methodology:
- Eliminate Disruptions: Ensuring a smooth operation without interruptions.
- System Flexibility: Being able to adapt to changes quickly.
- Excess Inventory Waste Elimination: Reducing inventory to expose problems and address them.
The Kaizen Philosophy: Continuous Improvement and Inclusivity
Kaizen, the Japanese term for 'improvement', embodies the principle of waste being the enemy and necessitates involvement from all organizational levels. It advocates for gradual, continuous improvement without significant investment, focusing on cost-effective enhancements.
Building Blocks of a Lean System
Lean systems are built on several foundations, including product design, small lot sizes, high-quality systems, concurrent engineering, and set up time reduction. These elements work in tandem to create a system that is efficient, adaptable, and quality-driven.
Quality Improvement and Work Flexibility
Quality defects can disrupt workflows, which is why lean operations emphasize defect prevention and flexibility. Techniques like autonomation help in detecting and addressing defects immediately. Guidelines for increasing flexibility include reducing downtime and cross-training workers.
The Rhythm of Lean: Tact Time and Load Leveling
'Tact time' refers to the pace at which work must be completed to meet customer demand, acting as the 'heartbeat' of a lean system. Load leveling ensures a stable daily schedule to manage capacity effectively.
Visual Systems and Kanban
Kanban, meaning 'signal', is a visual system that communicates demand requirements. It can take the form of a production kanban, signaling production needs, or a conveyance kanban, signaling delivery requirements to the next work center.
Limiting Work in Progress and Fostering Close Vendor Relationships
Lean operations aim to keep work in progress to a minimum, thereby reducing carrying costs and increasing flexibility. Close partnerships with a small number of suppliers are also crucial for frequent, quality deliveries.
Maintenance in Lean Systems
Maintaining equipment and facilities is vital to avoid disruptions. There are two categories of maintenance—reactive and proactive—with the latter being preferred in lean systems.
The Cost-Benefit Analysis of Preventative Maintenance
Preventative maintenance helps avoid breakdowns, reducing associated costs like loss of output and schedule disruptions. Optimal maintenance intervals can be calculated to balance costs and prevent failures.
Transitioning to a Lean System
To transition to a lean system, top management commitment is essential, along with worker cooperation and a plan to reduce setup times. Gradual conversion, starting from the end of the process, is recommended, along with preparing for obstacles such as resistance from management or suppliers.
In conclusion, lean operations and JIT systems are transformative strategies that can significantly enhance efficiency, quality, and cost management. Implementing these systems requires a holistic approach, considering product design, process optimization, and a culture of continuous improvement.
To explore these concepts further and learn more about lean operations and JIT practices, watch the original video on YouTube: Lean Operations and JIT.