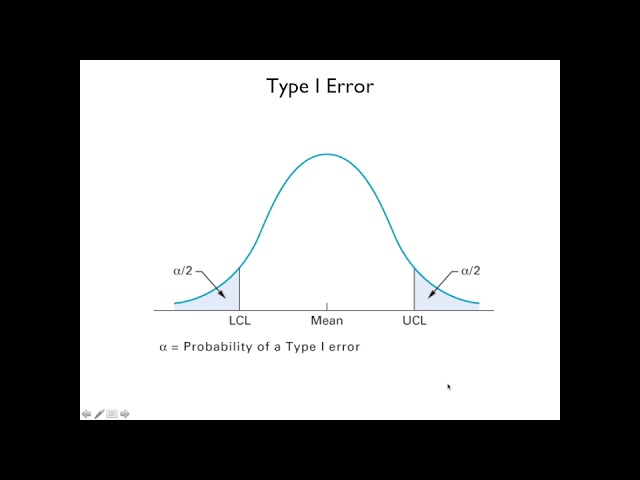
Create articles from any YouTube video or use our API to get YouTube transcriptions
Start for freeQuality Assurance Stages: An Overview
Quality Assurance (QA) is critical for maintaining standards in production and ensuring customer satisfaction. There are several stages in QA, each with its own methods and goals.
Acceptance Sampling
This is the initial phase of QA, involving inspections of production lots either before or after production. This traditional method focuses on detecting and rejecting defective products.
Process Control
Process control involves inspection and corrective action during the production process. It aims to prevent defects by monitoring and controlling the production process.
Continuous Improvement
The most progressive form of QA is when quality is built into the process. Continuous improvement focuses on preventing defects and improving the process over time.
Process Control and Its Importance
Process control is vital as it helps in maintaining consistent quality during production. It involves regular inspections and adjustments to the process to ensure that the final product meets the desired standards.
Where to Inspect in the Process
Selecting where to inspect in the process can significantly impact the efficiency of QA. Common inspection points include:
-
Raw Materials and Purchased Parts: Ensure the quality of materials before they enter the production process.
-
Before Costly Operations: Inspect components before an expensive process to avoid adding value to a defective product.
-
Before Irreversible Processes: For example, inspecting circuit boards before applying a conformal coating that is difficult to remove.
Centralized vs. On-Site Inspection
Deciding between centralized and on-site inspection depends on the nature of the tests required. Centralized inspections are better suited for specialized tests requiring specific equipment, while on-site inspections can be more efficient for simpler, visual checks.
Understanding Control Charts
Control charts are tools used in process control to determine if a process is within acceptable limits. They plot the data over time and show the upper and lower control limits.
Dealing with Errors
There are two main types of errors in process control:
-
Type 1 Error (Producer's Risk): Incorrectly concluding that a process is out of control when it is not.
-
Type 2 Error (Consumer's Risk): Failing to detect that a process is out of control when it is.
Mean and Range Charts
These charts help in identifying trends and variations in the process. The mean chart tracks the average of samples over time, while the range chart shows the dispersion of data.
Process Capability and Improvement
Process capability compares the output of a process to its specification limits. The goal is to reduce variability and ensure that the process consistently produces within the specified range.
Strategies for Improving Process Capability
-
Simplify and Standardize: Reducing complexity can lead to fewer errors.
-
Error-proofing: Designing the process to prevent mistakes.
-
Equipment Upgrades: Investing in better equipment can increase consistency and quality.
Taguchi Loss Function
The Taguchi loss function suggests that the cost associated with deviation from the target value increases as you move away from the target, even within the specification limits.
Acceptance Sampling
Acceptance sampling is a method used to determine if a batch of products meets certain standards. It is particularly useful when:
-
Time is Limited: When inspection of every item is not feasible due to time constraints.
-
Destructive Testing: When the inspection process destroys the item, like testing the functionality of bullets.
-
Inspection Fatigue: When inspecting large numbers leads to errors due to inspector fatigue.
Sampling Plans
Various sampling plans exist, including single, double, and multiple sampling plans. Each has specific criteria for determining if a lot should be accepted or rejected.
Operating Characteristic Curve
This curve helps in understanding the effectiveness of a sampling plan in discriminating between good and bad quality lots.
Risks in Acceptance Sampling
-
Customer's Risk (Beta): The risk that defective lots will be accepted.
-
Producer's Risk (Alpha): The risk of rejecting lots that meet the quality standards.
Conclusion
Quality control in manufacturing is a multi-faceted process that involves various strategies and tools to ensure that products meet the required standards. From the initial acceptance sampling to the continuous improvement of processes, QA is an ongoing effort that significantly impacts customer satisfaction and operational efficiency.
To learn more about each of these stages and how they contribute to a comprehensive quality control strategy, watch the full video here.