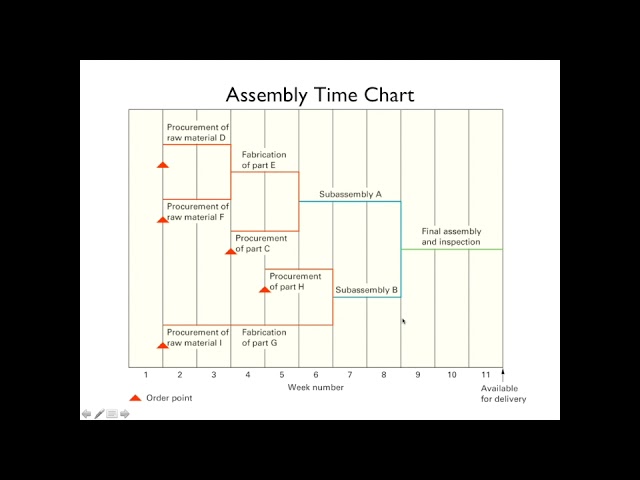
Create articles from any YouTube video or use our API to get YouTube transcriptions
Start for freeUnderstanding Dependent vs. Independent Demand in Supply Chain Management
In the realm of supply chain management, distinguishing between dependent and independent demand is fundamental. Independent demand typically exhibits stability, though it may experience minor fluctuations. Managing such demand involves maintaining a safety stock buffer—inventory that covers demand during the replenishment cycle. When demand descends to the safety stock level, a new order is placed, ensuring continuous availability of products.
Conversely, lumpy or dependent demand occurs sporadically, in bursts, often triggered by specific orders or events. Predictability in such demand patterns enables precise ordering—acquiring inventory precisely when needed, without surplus.
Material Requirements Planning (MRP): A Computer-Based Inventory Management System
Material Requirements Planning (MRP) is a computer-based system that optimizes inventory management by analyzing the master production schedule, end item requirements, and time-phased needs for sub-assemblies, components, and raw materials. MRP aims to answer three pivotal questions:
- What items are needed?
- In what quantities?
- When should they be ordered?
The MRP process involves several inputs:
- A master schedule detailing production timelines
- Current and future orders
- Forecasts predicting demand
- Design changes impacting the Bill of Materials (BOM)
These inputs feed into the MRP software, which churns out essential reports such as order releases, planned order schedules, and inventory transactions.
Delving into MRP Outputs and Reports
MRP systems generate various reports that guide inventory management decisions:
- Primary reports include changes in inventory levels, order releases, and planned order schedules.
- Secondary reports encompass exception reports, planning reports, and performance control reports.
The Importance of Cumulative Lead Time
Cumulative lead time represents the total time required from placing an order to the completion of the final product. It includes lead times for order placement, fabrication, sub-assembly, and final assembly. Understanding cumulative lead time is essential for scheduling orders and ensuring timely product availability.
Product Structure Tree and Assembly Time Chart
A product structure tree visually represents the components and sub-assemblies that combine to form a final product. An assembly time chart, on the other hand, outlines the production schedule in reverse, from final assembly to procurement of raw materials, ensuring that all parts are ordered and fabricated at the correct times to meet production schedules.
MRP Considerations: Safety Stock and Load Reports
Although MRP ideally eliminates the need for safety stock, maintaining a buffer is strategic for dealing with bottlenecks, scrap rates, and variability in lead times. Safety time—a buffer period ensuring earlier receipt of materials—mitigates risks of shortages.
Load reports provide insights into production capacity, highlighting when the manufacturing process may exceed capacity and suggesting adjustments to smooth out production loads.
Enterprise Resource Planning (ERP): The Backbone of Integrated Business Processes
Enterprise Resource Planning (ERP) systems serve as centralized databases integrating various business functions:
- Accounting and Finance: Manages financial records and transactions.
- Marketing: Supports lead generation and targeted marketing efforts.
- Human Resources: Stores employee data and manages performance evaluations.
- Purchasing: Handles vendor relations and purchase decisions.
- Production Planning: Incorporates MRP for inventory management.
- Inventory Management: Tracks inventory requirements and availability.
- Sales: Manages order information and shipping details.
- Supply Chain Management: Enhances visibility and management of the supply chain network.
An ERP system can either encompass an MRP module or interface with it, creating a seamless flow of information across the organization.
In Conclusion: Navigating Supply Chain Complexity with MRP and ERP
In summary, understanding the distinction between dependent and independent demand is vital for effective inventory control. MRP systems provide structured approaches to manage material requirements, while ERP systems offer comprehensive business integration. Together, they form a robust framework for navigating the complexities of supply chain management.
For a deeper dive into the nuances of MRP and ERP, you can access the full YouTube video lecture here.