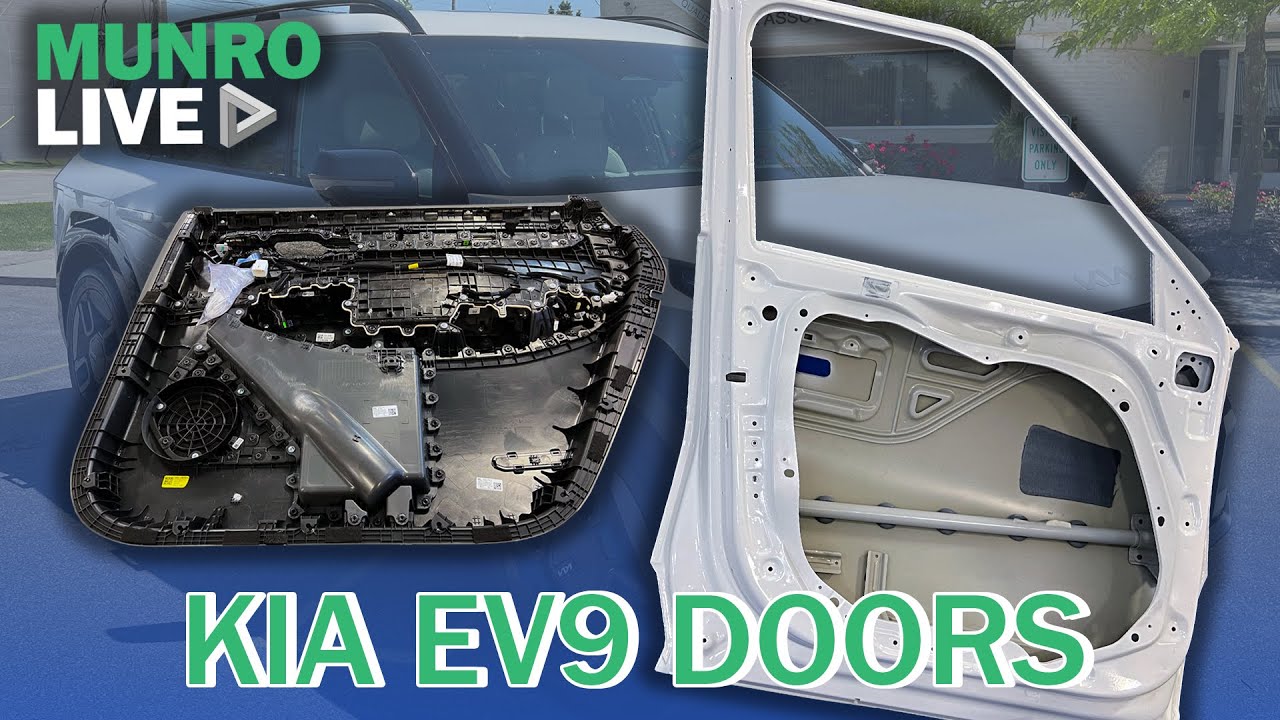
Create articles from any YouTube video or use our API to get YouTube transcriptions
Start for freeKia EV9 Door Construction: A Closer Look
The Kia EV9, a new electric vehicle in the market, has been the subject of a recent teardown analysis. This process allows for a detailed examination of its components, manufacturing methods, and design choices. One of the key areas of focus in this analysis is the vehicle's doors, which provide significant insights into the overall construction and engineering philosophy behind the EV9.
Traditional Stamped Steel vs. Cybertruck's Stainless Steel
The EV9's doors are constructed using traditional stamped steel, which differs significantly from the approach taken by Tesla's Cybertruck. The stamped steel construction allows for a hemmed metal design around the perimeter of the door. This means that the outer skin and inner door structure are brought together, with the outer structure folding around to capture the inner structure.
In contrast, the Cybertruck's unique thick stainless steel exterior prevented this type of construction. The material could not be stamped or machined to create a 180-degree bend, necessitating laser welding around the entire perimeter of the door.
Weight Considerations: Steel vs. Aluminum
The choice of steel for the EV9's doors results in a weight of approximately 20 kg per door. This is notably heavier than comparable aluminum doors, such as those found in the Rivian R1T, which weigh only about 11 kg. The decision to use steel over aluminum involves a trade-off between weight savings and material costs.
Aluminum doors offer significant weight reduction, which can benefit overall vehicle efficiency and battery range. However, they come with higher material costs and potentially more complex manufacturing processes. Automakers must carefully consider these factors when deciding between steel and aluminum construction.
The Paradox of Weight Savings
Interestingly, the automotive industry sometimes faces a paradox when it comes to weight savings. Engineers often work hard to reduce the weight of individual components, including doors, only to have additional weight added back in during the final assembly process. This is done to achieve a desired "feel" when closing the door, often described as a satisfying "clunk."
This practice highlights the complex balance between engineering efficiency and consumer expectations. It also raises questions about the overall approach to vehicle design and whether a more holistic view could lead to better outcomes.
Crash Beam Design and Manufacturing
The EV9's doors feature an internal structural member known as a crash beam or anti-intrusion beam. This component plays a crucial role in protecting occupants during side-impact collisions.
Kia's Approach: Simple and Cost-Effective
In the Kia EV9, the crash beam is constructed from a simple piece of tubular steel. This design choice offers several advantages:
- Easy manufacturing: The beam can be produced by simply cutting steel tubing to the required length.
- Low cost: The simplicity of the design translates to lower production costs.
- Straightforward installation: The beam can be easily welded or adhered in place within the door structure.
Comparison with Hyundai Ioniq
It's interesting to compare the EV9's crash beam design with that of the Hyundai Ioniq, which is part of the same automotive family. The Ioniq uses a stamped metal design for its crash beam, which presents a different set of trade-offs:
- Potentially lower weight: The stamped design may result in a lighter component compared to the tubular steel used in the EV9.
- Higher manufacturing costs: The stamping process is generally more expensive than simple tube cutting.
- Different space utilization: The stamped design may allow for a different profile within the door, potentially freeing up space for other components.
This comparison illustrates how even closely related vehicles can take different approaches to solving the same engineering challenge.
Door Modules: Front vs. Rear Differences
One of the most intriguing aspects of the EV9's door design is the difference between the front and rear door modules.
Front Door Module
The front door of the EV9 features a modular design similar to what was observed in the Cybertruck. This module includes:
- Integrated handles molded directly into the injection-molded component.
- A comprehensive structure that houses various door mechanisms.
- An all-in-one design that simplifies assembly by allowing the entire module to be installed as a single unit.
Rear Door Module
Surprisingly, the rear door of the EV9 does not use the same modular approach. Instead, it employs a more traditional design:
- The window guide and mechanism are bolted directly through the door.
- This requires a "blind install" process, where components must be carefully positioned and secured without the benefit of a pre-assembled module.
- The motor for the window mechanism is located at the bottom of the door.
Speculating on the Design Difference
The stark contrast between the front and rear door designs raises questions about the development process. Some possible explanations include:
- Different development teams or timelines for front and rear doors.
- Carry-over designs from other vehicle platforms, particularly for the rear doors.
- Cost considerations for a potentially lower-volume three-row vehicle.
This difference in approach between front and rear doors highlights the complex decision-making processes involved in vehicle design and manufacturing.
Window Track Integration: An Improvement over Cybertruck
The EV9's door module demonstrates an improvement in design efficiency compared to the Cybertruck, particularly in how the window tracks are integrated.
Cybertruck's Approach
In the Cybertruck, the door module and window tracks were separate components:
- Metal tracks with a cable system were attached to the back of a plastic panel.
- This design required additional assembly steps to bring these components together.
- The use of different materials (metal and plastic) for parts that don't move relative to each other goes against some principles of efficient design.
EV9's Integrated Design
The Kia EV9 takes a more integrated approach:
- The metal rail that guides the window mechanism is molded directly into the plastic panel of the door module.
- Only the cables and retainers need to be added separately.
This design offers several advantages:
- Cost savings through reduced parts and assembly steps.
- Labor savings in the manufacturing process.
- Potential improvements in reliability due to fewer separate components.
This integration showcases how continuous improvement and rethinking of component design can lead to more efficient manufacturing processes.
Glass Attachment Methods
The method of attaching the window glass to the door module is another area where the EV9 shows some interesting design choices.
Comparison with Traditional Methods
In many vehicles with full-framed doors, the glass attachment doesn't need to be extremely secure because the glass rides inside a track in the door frame. For example, in the Ford F-150, the glass simply snaps into attachment features on the door module through holes in the glass.
EV9's Approach
The Kia EV9 uses a different method:
- One side of the glass has a threaded attachment point.
- The other side uses a "gripper panel" that clamps onto the glass.
This method is more labor-intensive and potentially more expensive than simpler snap-in designs. It's not immediately clear why this more complex approach was chosen for a full-framed door design.
Door Latch and Handle Mechanism
While not analyzed in depth, the door latch and handle mechanism of the EV9 appears to be quite complex. The multitude of functions and mechanical features in this assembly suggest a sophisticated design that may offer advanced functionality but could also present challenges in terms of manufacturing and long-term reliability.
Lower Door Cladding: A Point of Contention
One design feature that drew criticism in the analysis is the lower door cladding of the EV9.
Design and Assembly
- The lower skin of the door is stamped to provide attachment points for a decorative component.
- This requires plugging holes in the door skin, necessitating additional sealing measures.
- The assembly involves multiple pieces: high-gloss upper molding, matte lower section, and a painted decorative insert.
Criticisms of this Approach
- Increased complexity and cost due to multiple components and assembly steps.
- Potential for damage and difficult repairs - if hit, these components often need complete replacement rather than repair.
- Environmental concerns due to the use of multiple materials that are challenging to recycle or dispose of properly.
This design choice highlights the ongoing tension in automotive design between aesthetic considerations and practical, cost-effective manufacturing.
Interior Trim Manufacturing Methods
The analysis also touched on the manufacturing methods used for interior trim components, particularly focusing on the doors.
"Taco Bell" Interiors
The term "Taco Bell Interiors" was used to describe a common approach in automotive design where similar basic components are combined in different ways to create seemingly unique interiors. This typically involves:
- Thermoformed or vacuum-formed skins for a soft-touch feel.
- Various inserts and sewn wrapped components.
- Injection-molded plastic for lower sections.
EV9's Interior Door Panel Construction
The EV9's door panels reveal a mix of manufacturing techniques:
- A combination of screws and weld points are used to assemble components.
- The process likely involves a pre-assembly step using screws, followed by welding in a fixture.
- This approach balances the need for precise assembly with efficient manufacturing processes.
Comparison with Tesla Model Y
The Tesla Model Y takes a different approach to door panel assembly:
- No screws are used; all components are welded together.
- Parts are loaded loose into a fixture and welded in one or two steps.
- This method requires more sophisticated fixturing and capital equipment but can be more efficient in high-volume production.
Vinyl Application Techniques
The analysis also highlighted the methods used to apply vinyl coverings to interior panels:
- Foam-backed vinyl is thermally formed onto panels.
- Small holes in the panels allow air to escape during the forming process.
- Textures and grains are imparted to the vinyl during the forming process.
- Special techniques are used to secure edges and corners without visible defects.
This detailed look at manufacturing processes provides insight into the complexities of automotive interior design and the trade-offs between aesthetics, cost, and production efficiency.
Conclusion: Balancing Act in Automotive Design
The analysis of the Kia EV9's doors and related components reveals the intricate balancing act that automotive manufacturers must perform. Every decision, from material choice to assembly method, involves trade-offs between cost, weight, manufacturability, and consumer appeal.
Key takeaways from this analysis include:
- Material choices significantly impact weight and cost, with steel offering cost benefits and aluminum providing weight savings.
- Manufacturing methods vary widely, even within the same vehicle, highlighting the complexity of automotive design.
- Integration of components, as seen in the EV9's door module improvements, can lead to significant efficiencies.
- Aesthetic choices, such as lower door cladding, can sometimes conflict with practical manufacturing and repair considerations.
- Interior trim manufacturing involves a complex interplay of materials and processes to achieve desired looks and feels.
Ultimately, this analysis underscores the importance of holistic thinking in automotive design. While individual components may be optimized, the overall impact on the vehicle's cost, performance, and consumer appeal must always be considered. As the automotive industry continues to evolve, particularly with the shift towards electric vehicles, these design and manufacturing decisions will play a crucial role in determining which vehicles succeed in the marketplace.
The Kia EV9 represents just one approach to these challenges, and it will be fascinating to see how these design philosophies evolve in future models and across different manufacturers. As consumers become more aware of the engineering behind their vehicles, understanding these design choices may also influence purchasing decisions and brand loyalty in the competitive electric vehicle market.
Article created from: https://youtu.be/RtUc_sdsHhA?feature=shared